Токарная обработка металла предполагает изготовление металлических изделий с заранее определенными размерами путем последовательных снятий слоёв металла с заготовки. Как правило, это происходит во время вращения заготовки при помощи инструмента с твердой режущей кромкой (резца) и его перемещения как в продольном, так и поперечном направлениях.
Виды токарных работ — это черновое, получистовое и чистовое точение, сверление отверстий и растачивание внутренних поверхностей, точение конуса и отрезка заготовки, обработка торца, нарезание внешних и внутренних резьб, а также точение поверхностей фасонного типа и др. Кроме того, эти виды работ подразделяются еще и на более мелкие подоперации.
Виды токарных работ — это черновое, получистовое и чистовое точение, сверление отверстий и растачивание внутренних поверхностей, точение конуса и отрезка заготовки, обработка торца, нарезание внешних и внутренних резьб, а также точение поверхностей фасонного типа и др. Кроме того, эти виды работ подразделяются еще и на более мелкие подоперации.
Основные типы резцов
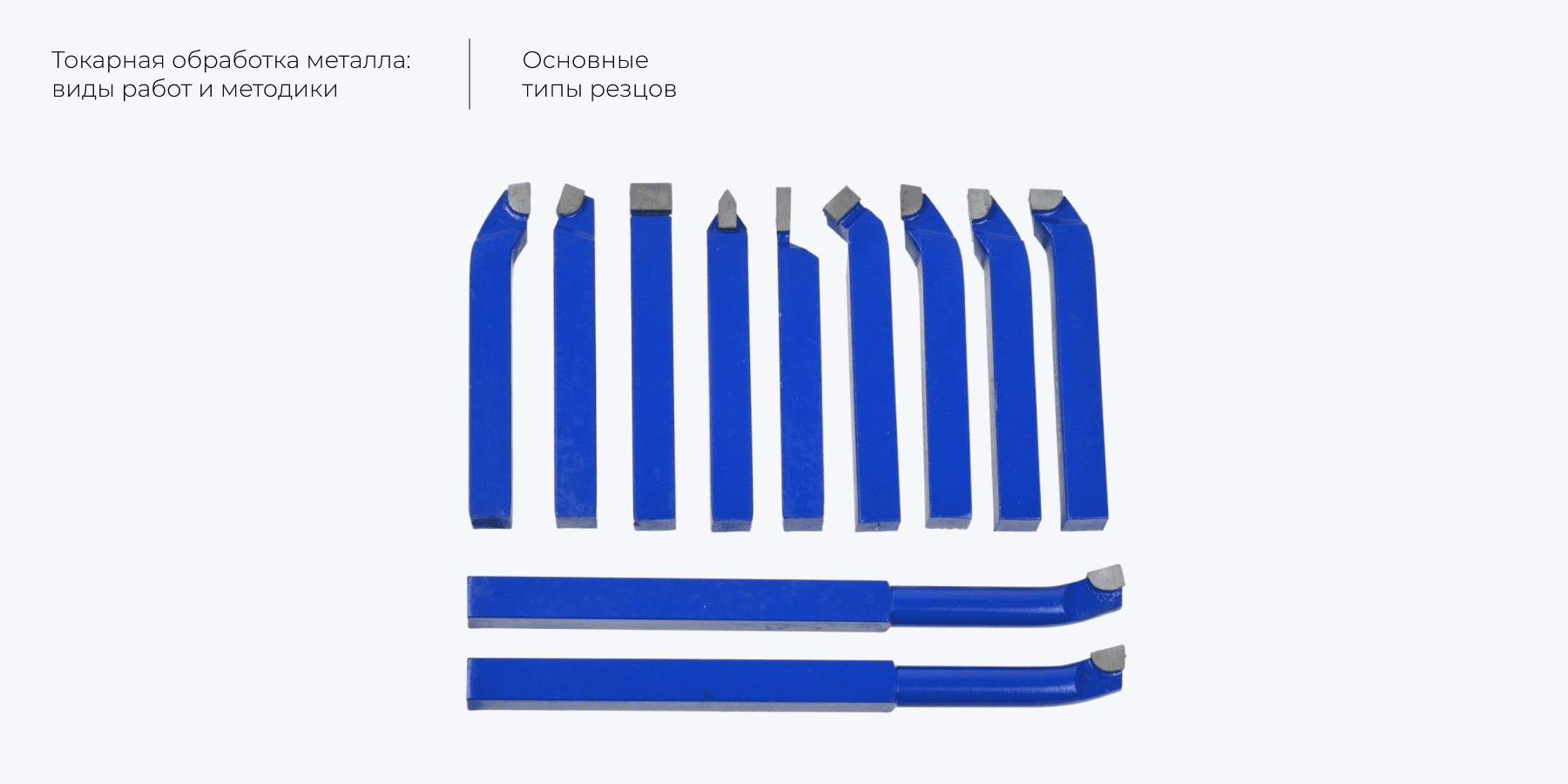
Обеспечение всех этих работ производится с использованием различных инструментов — резца для определенных токарных операций, сверла, зенкера, развертки и т.д.
Резцы подразделяются на несколько типов:
- проходной применяется для обработки внешней цилиндрической поверхности, а отогнутый проходной резец при поперечной подаче может обрабатывать торец заготовки;
- проходной упорный применяется для обработки ступенчатых деталей;
- подрезной используется для подрезания торцов, буртиков, для проточки детали ступенчатого профиля;
- расточной — для увеличения диаметра отверстий сделанных при помощи сверла;
- отрезной служит для отрезки детали от заготовки, для протачивания пазов, канавок; обработка детали этим резцом производится под прямым углом к заготовке;
- резьбовой служит для нарезания внутренней и наружной резьб (при перемещении резца вдоль заготовки с одинаковой скоростью оставляет на металле спиралевидную линию);
- фасонные резцы — для обработки поверхностей деталей сложных форм.
Сами резцы бывают: цельными, с напайными твердосплавными пластинами и сборными (со сменными пластинами, которые легко и быстро заменяются одна другой).
Скорости токарного станка
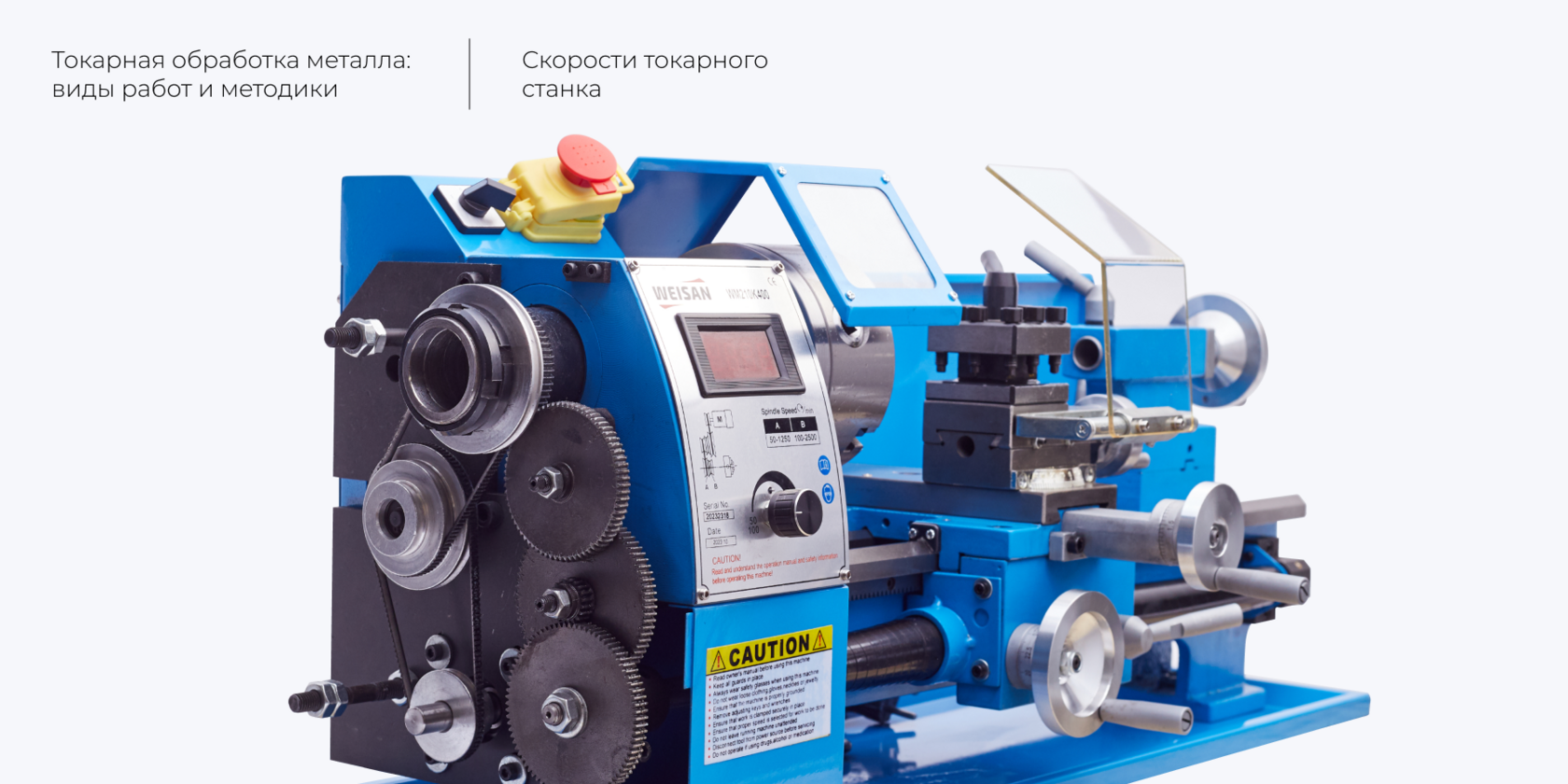
Токарные станки WEISAN имеют два диапазона скоростей (скорость токарного станка — это количество оборотов шпинделя в минуту):
а) от 50 до 1500 оборотов в минуту;
б) от 100 до 2500 об./мин.
Первый диапазон скорости используется в качестве силовой обработки заготовки, второй — скоростной. Оптимальная скорость резания обрабатываемой детали прежде всего зависит от твердости обрабатываемого материала. Обработка твердых металлов производится на относительно низкой скорости резания, чем при обработке более мягких металлических изделий. Как правило, на более низких скоростях производится черновая обработка детали, а для достижения чистой гладкой поверхности обычно используются высокие скорости.
Кроме того выбор скорости резания зависит от режущего инструмента. Резцы из твердого сплава могут работать на повышенных скоростях, если использовать во время работы СОЖ.
Кроме того выбор скорости резания зависит от режущего инструмента. Резцы из твердого сплава могут работать на повышенных скоростях, если использовать во время работы СОЖ.
Обработка цилиндрических поверхностей
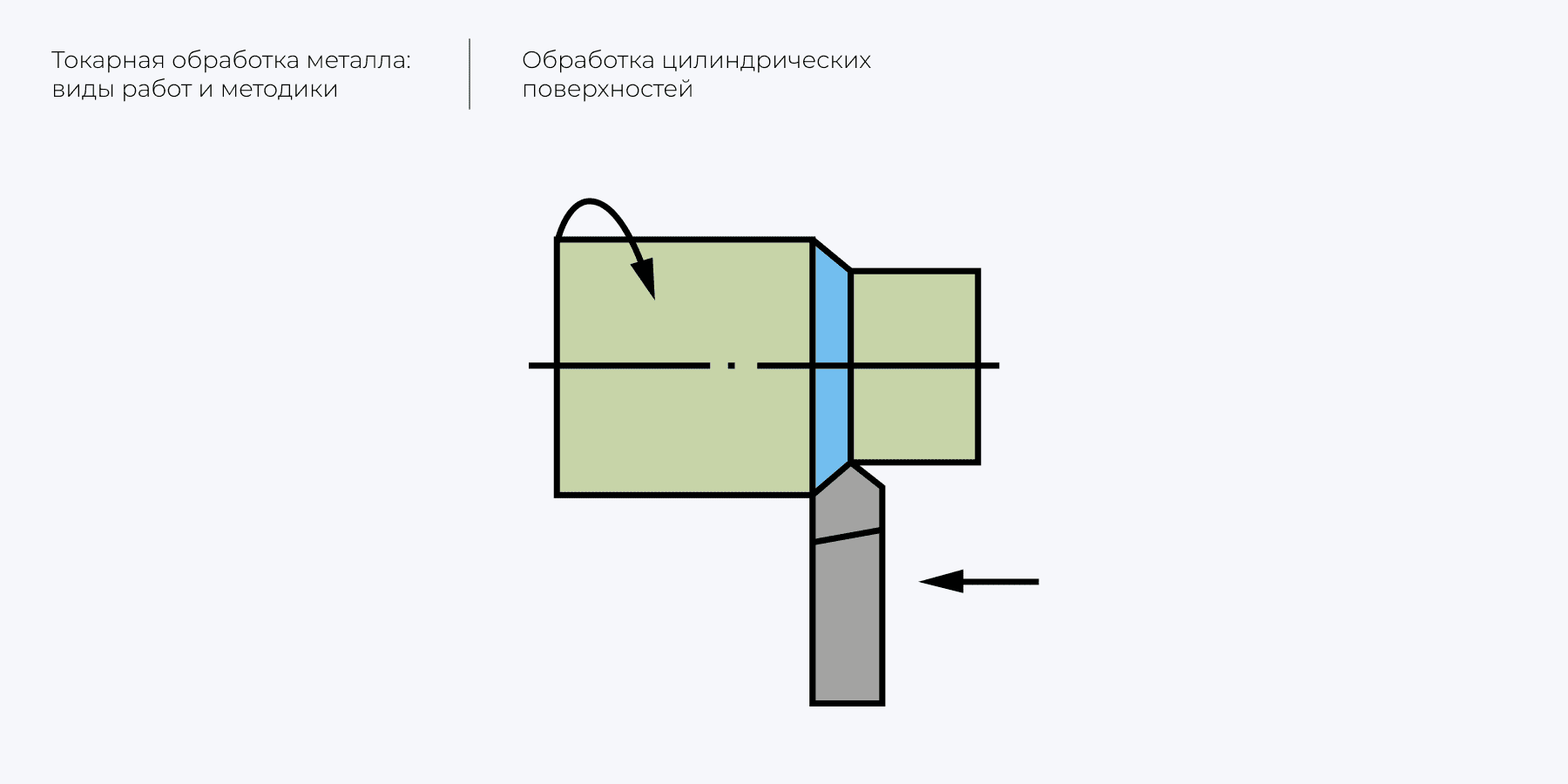
При обработке цилиндрических поверхностей основным методом является токарная обработка. На токарном станке заготовка вращается, а режущий инструмент (резец) перемещается вдоль оси заготовки, постепенно снимая слой металла. Для достижения высокого качества и точности поверхности также применяется шлифование, при котором шлифовальный круг движется вдоль оси вращающейся заготовки.
Резцы бывают разных типов: для черновой обработки используются более грубые резцы, которые снимают большие слои материала, а для чистовой обработки применяются более точные инструменты, обеспечивающие гладкую поверхность. Шлифовальные круги также выбираются в зависимости от требуемой чистоты поверхности.
Для черновой обработки скорость подачи составляет около 0,2-0,5 мм на оборот, а для чистовой обработки — 0,05-0,2 мм на оборот.
Обработка торцевых поверхностей
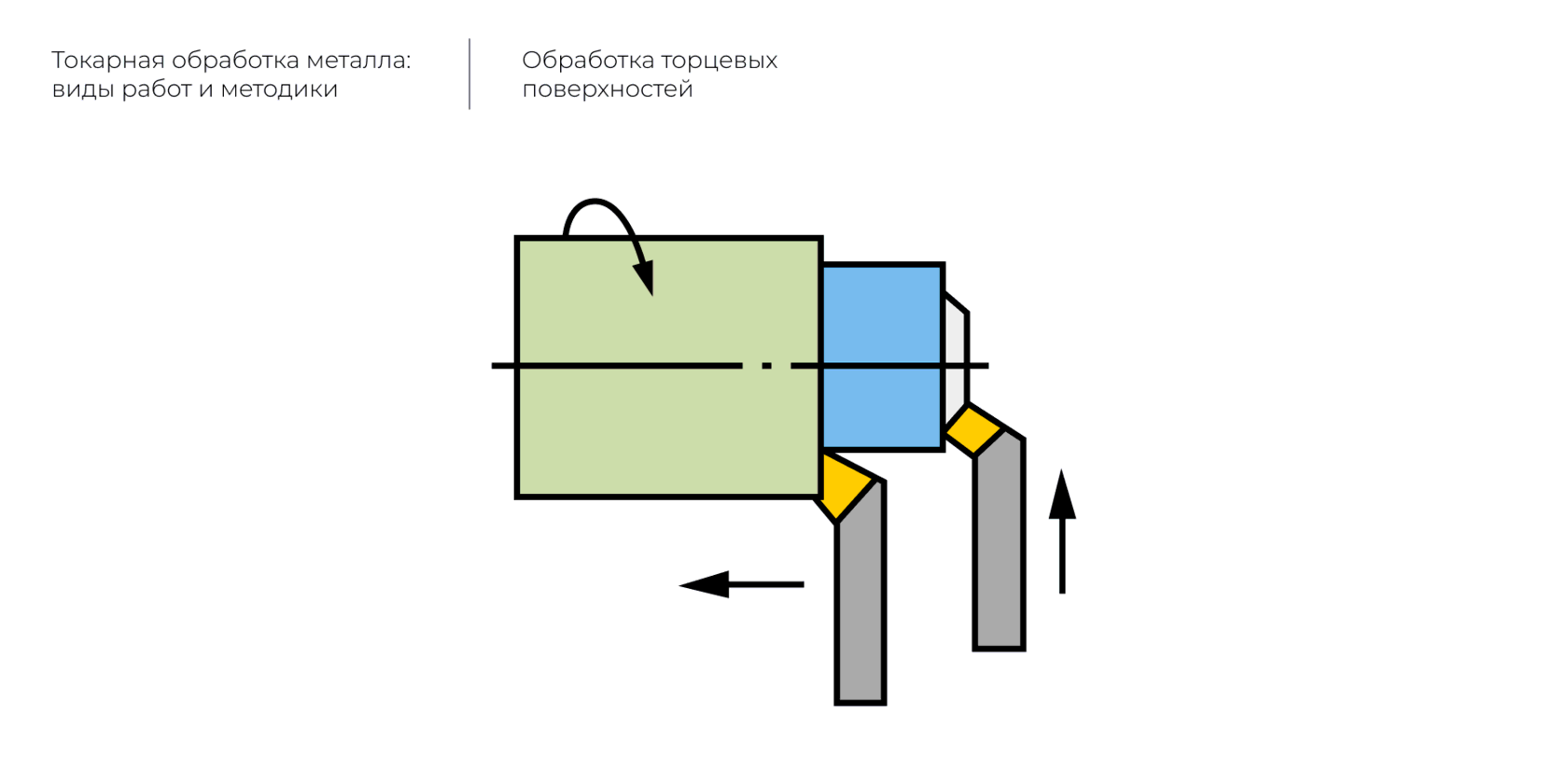
Обработка торцевых поверхностей может выполняться как на токарном станке, так и с помощью фрезерования. В первом случае заготовка вращается, а резец перемещается перпендикулярно оси заготовки. При фрезеровании плоские фрезы движутся по плоскости торцевой поверхности, снимая слой металла.
Для этой работы используются торцевые резцы и фрезы. Скорость подачи для черновой обработки составляет 0,15-0,3 мм на оборот, а для чистовой — 0,05-0,1 мм на оборот.
Обработка конических поверхностей (конусов)
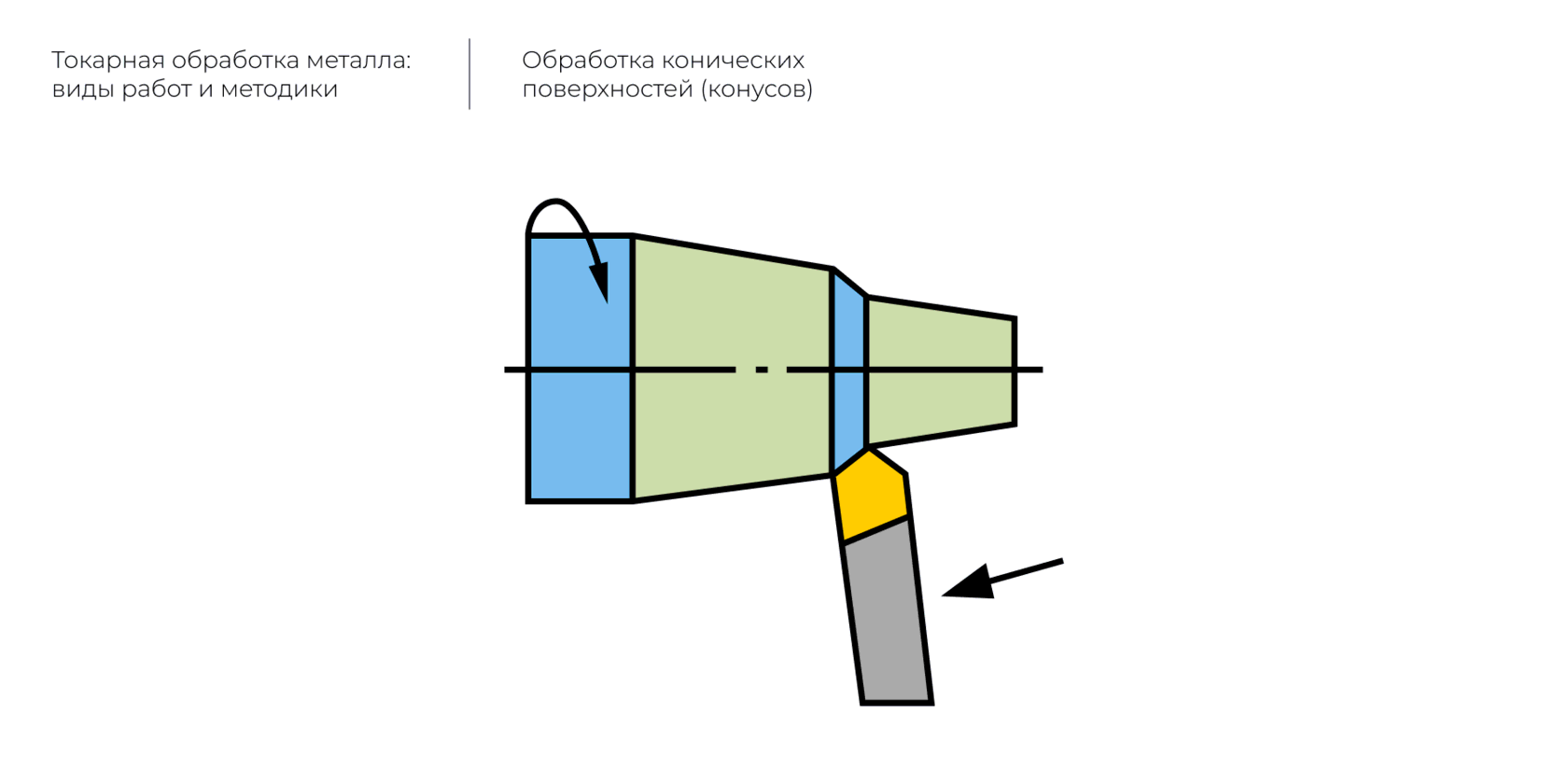
При обработке конических поверхностей резец движется вдоль оси под углом, создавая конусную форму. Можно также использовать конусные фрезы при фрезеровании.
Для этой работы применяются токарные резцы с выдвинутой вперёд режущей кромкой острой формы. Скорость подачи для черновой обработки составляет 0,1-0,3 мм на оборот, а для чистовой — 0,05-0,1 мм на оборот. Важно правильно настроить угол поворота малой продольной подачи и регулярно проверять параметры заготовки и точность углов, чтобы получить деталь с заданными размерами.
Обработка канавок
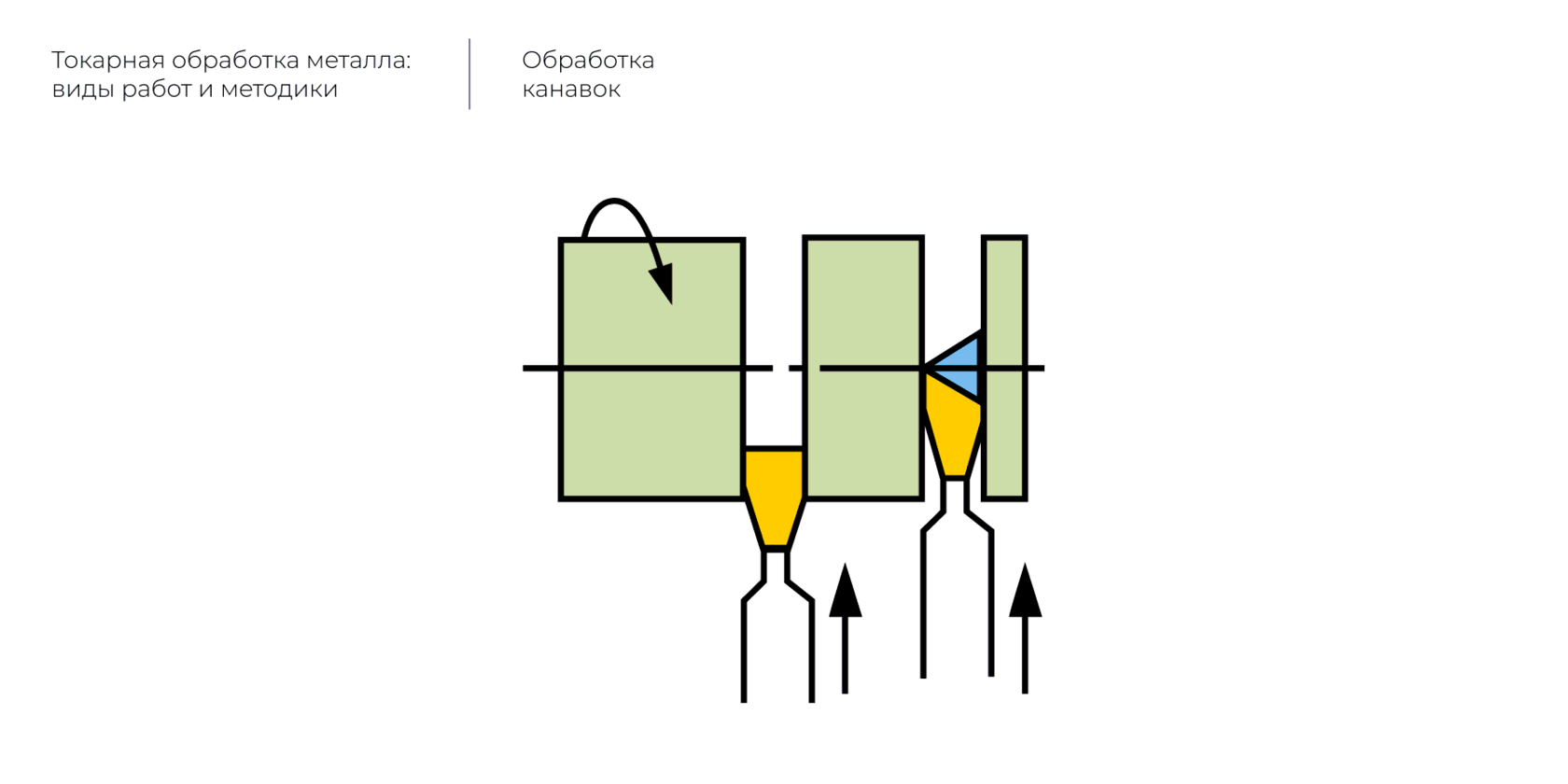
Канавки в металле можно делать как на токарном станке, так и с помощью фрезерования. На токарном станке для этого используется специальный канавочный резец, а при фрезеровании — дисковые или торцевые фрезы.
Скорость подачи для черновой обработки составляет 0,1-0,25 мм на оборот, а для чистовой — 0,05-0,15 мм на оборот. Важно правильно выбрать тип резца, чтобы минимизировать его износ и обеспечить необходимую глубину и ширину канавки. Постоянный контроль за состоянием инструмента и параметрами канавки помогает достичь высокого качества обработки.
Обработка отверстий
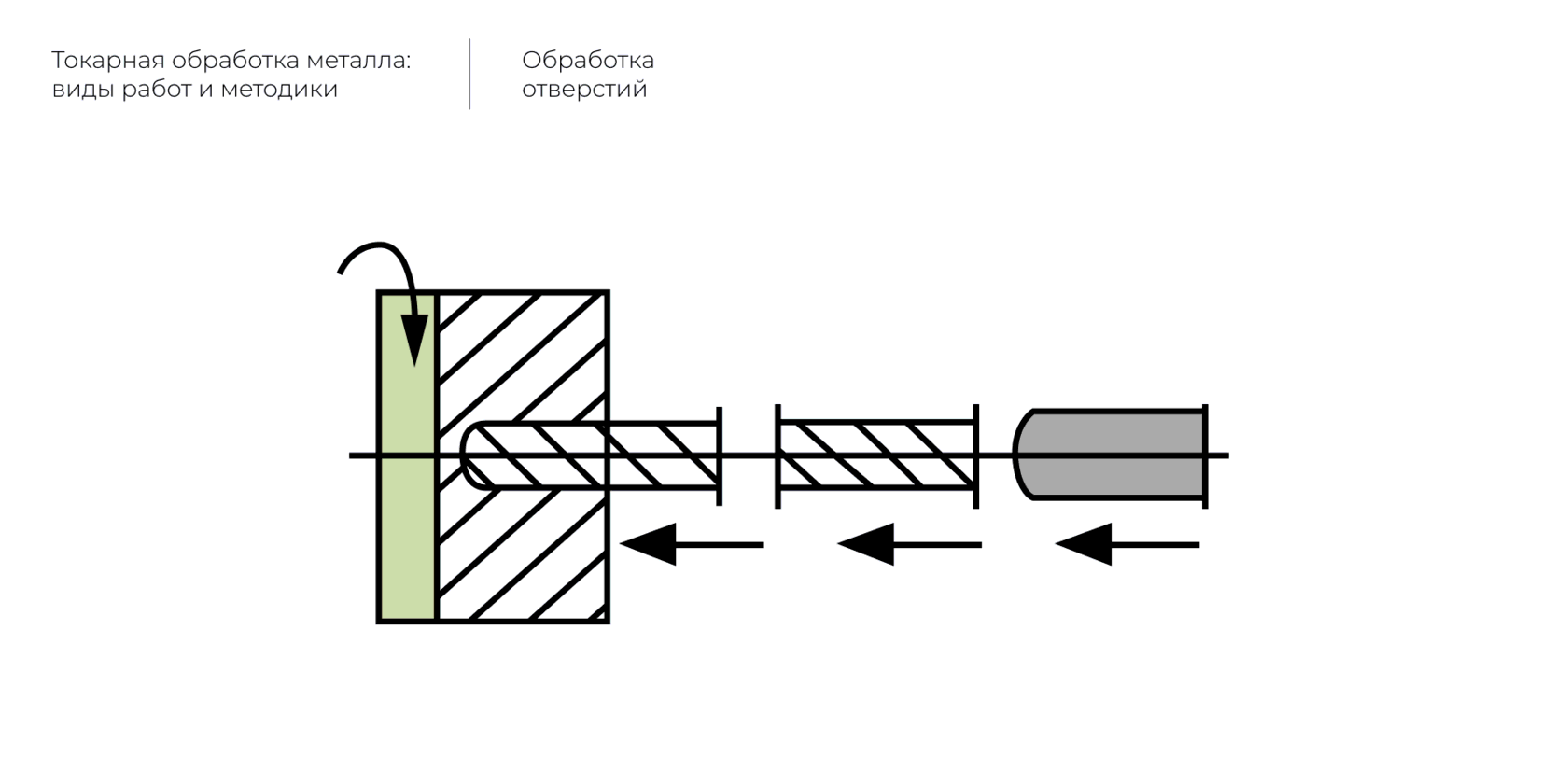
Для создания и обработки отверстий применяется несколько методов: сверление, расточка и развёртывание. Сверление — это основной метод, при котором используется сверло для создания отверстия в заготовке. Расточка применяется для увеличения диаметра уже существующих отверстий с помощью специального расточного инструмента, а развёртывание — для улучшения качества поверхности и точности размеров.
При сверлении используются спиральные и центровочные сверла, для расточки — расточные резцы и оправки, а для развёртывания — развёртки. Скорость подачи при сверлении составляет 0,05-0,3 мм на оборот, при расточке — 0,1-0,25 мм на оборот, а при развёртывании — 0,02-0,1 мм на оборот. Проверка и коррекция размеров отверстий после каждой операции позволяют добиться высокой точности и качества обработки.
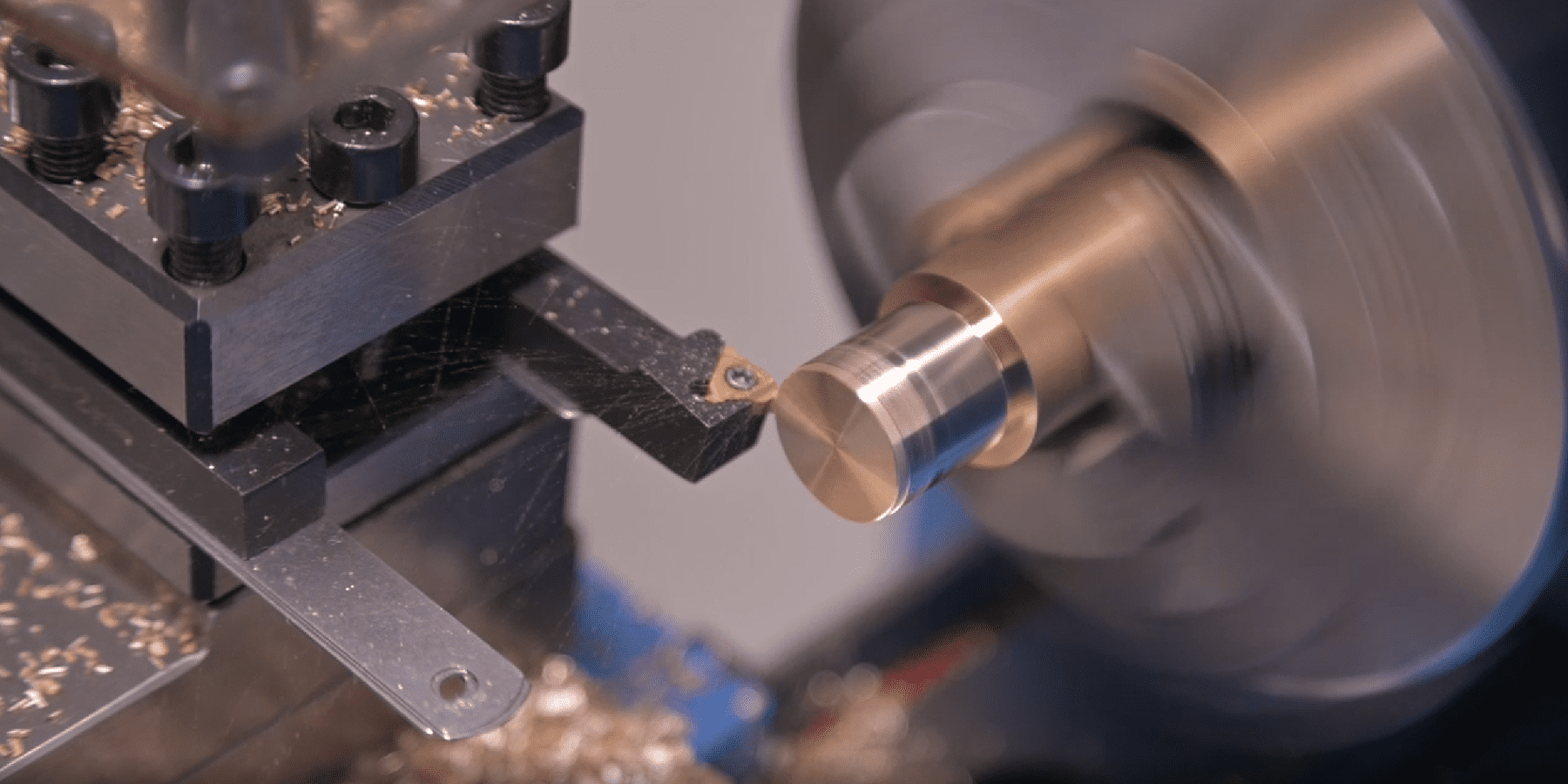
Итак, хорошо заточенный и правильно подобранный для определенной токарной операции инструмент обеспечивает оптимальное качество обработки изделия. Также огромную роль в этом процессе играют правильный выбор скорости подачи и регулярное использование охлаждающей жидкости, позволяющей избегать перегрева как заготовки, так и резца. Все это положительно отражается на качестве изделия и на долговечности инструмента. А работа при этом приносит истинное удовлетворение!